在工業制造的浩瀚宇宙中,鋼鐵材料猶如支撐萬物的星辰,而熱處理工藝則是賦予其獨特性能的 "基因編輯術"。從精密儀器的微型螺栓到萬噸級設備的承重構件,標準件的性能優劣直接決定著整個系統的可靠性。據統計,經過科學熱處理的標準件使用壽命可提升 3-5 倍,而因熱處理不當導致的失效案例占工業事故的 40% 以上。本文將系統解構鋼的熱處理核心工藝,并深度剖析標準件生產中如何通過精準工藝控制實現等級與性能的雙重躍升,為制造業同仁提供從理論到實踐的全流程技術指南。
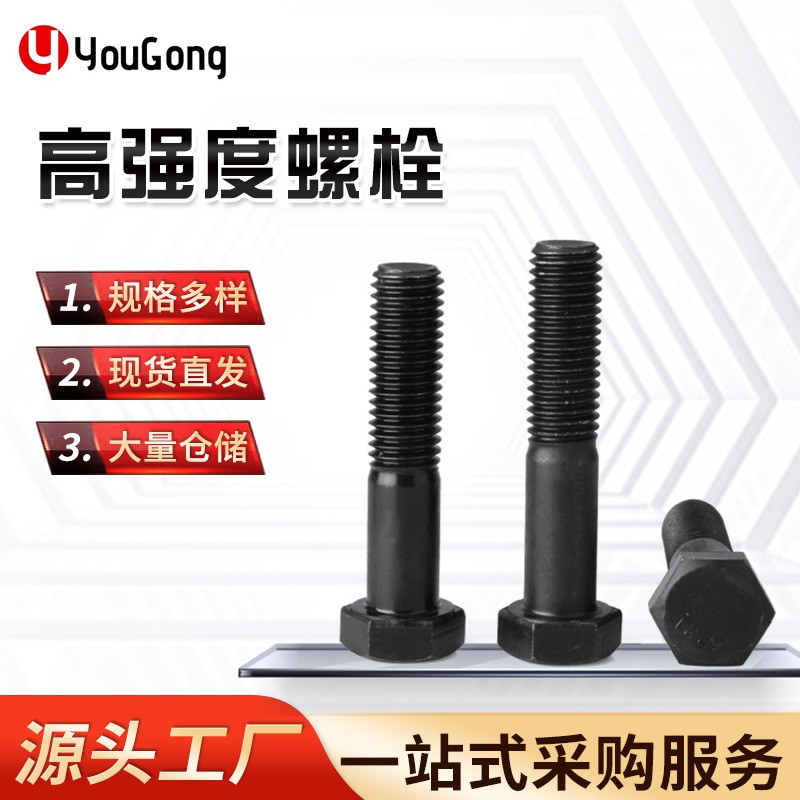
熱處理是指金屬在固態下通過加熱、保溫、冷卻的工藝循環,改變內部顯微組織,從而獲得所需性能的技術過程。這一過程猶如為鋼鐵注入 "性格特質"—— 退火賦予其溫柔韌性,淬火使其剛硬不屈,回火則調和剛柔并濟。
加熱的核心目標是使鋼件形成均勻細小的奧氏體組織。以共析鋼為例,當溫度升至 Ac1(727℃)以上時,珠光體向奧氏體的轉變經歷四個階段:
形核階段:奧氏體晶核優先在鐵素體與滲碳體相界處形成,利用晶界處的能量、結構及成分起伏
長大階段:通過鐵原子晶格改組(bcc→fcc)和碳原子擴散,奧氏體向兩側擴展
殘余滲碳體溶解:鐵素體先于滲碳體消失,未溶滲碳體需延長保溫時間完全溶解
成分均勻化:通過碳原子擴散消除濃度梯度,獲得均質奧氏體
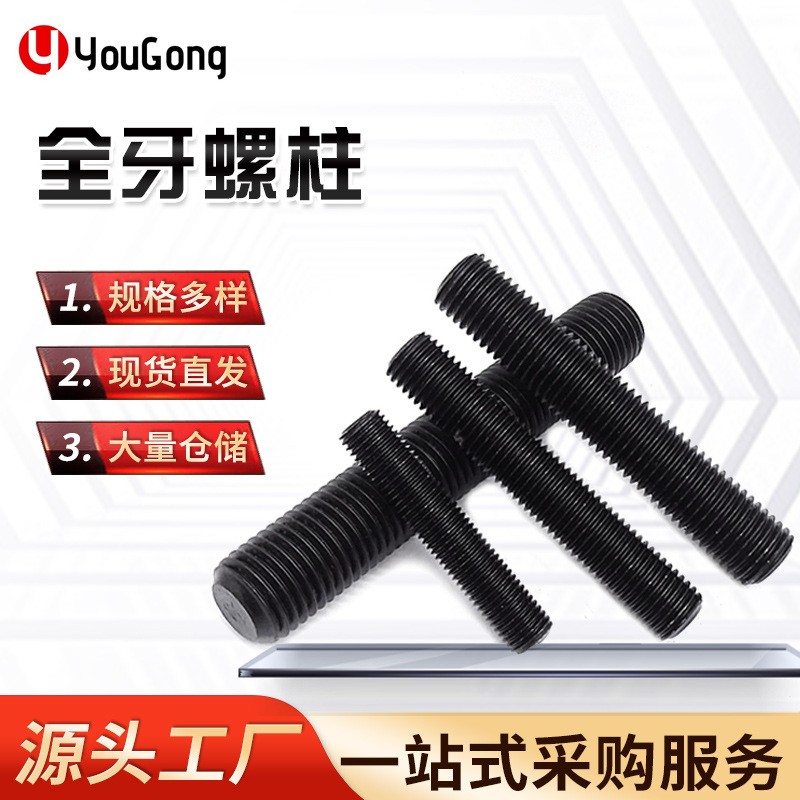
保溫時間需滿足兩個要求:
冷卻速度直接決定奧氏體轉變產物:
鐵碳合金相圖是熱處理工藝的 "導航地圖",其中關鍵臨界點包括:
實際熱處理中,由于相變滯后效應,加熱時需達到 Ac1、Ac3、Accm,冷卻時則為 Ar1、Ar3、Arcm。以 45 鋼為例,其淬火溫度通常設定為 Ac3+30-50℃(840-860℃),確保鐵素體完全溶入奧氏體,避免未溶鐵素體降低硬度。
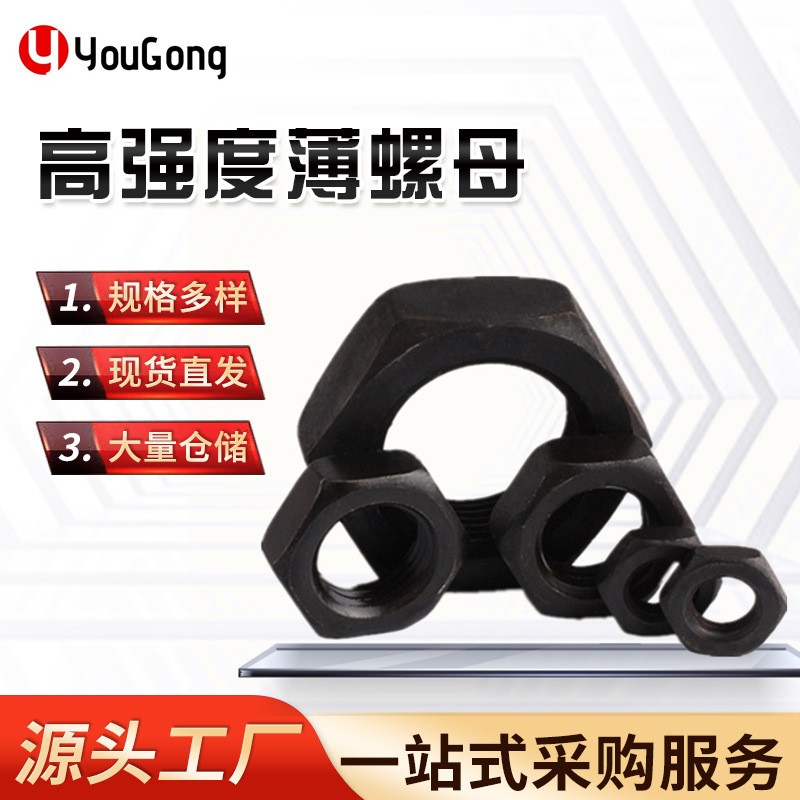
退火工藝如同為鋼鐵 "修身養性",根據目的不同分為:
完全退火:加熱至 Ac3+30℃,適用于亞共析鋼,細化晶粒、消除鍛造應力
球化退火:加熱至 Ac1 附近,使滲碳體球狀化,獲得粒狀珠光體,改善切削性能(如軸承鋼 GCr15)
去應力退火:加熱至 500-650℃,消除焊接 / 切削加工應力,防止變形開裂
等溫退火:在奧氏體化后快速冷卻至珠光體轉變區等溫,縮短工藝時間 30-50%
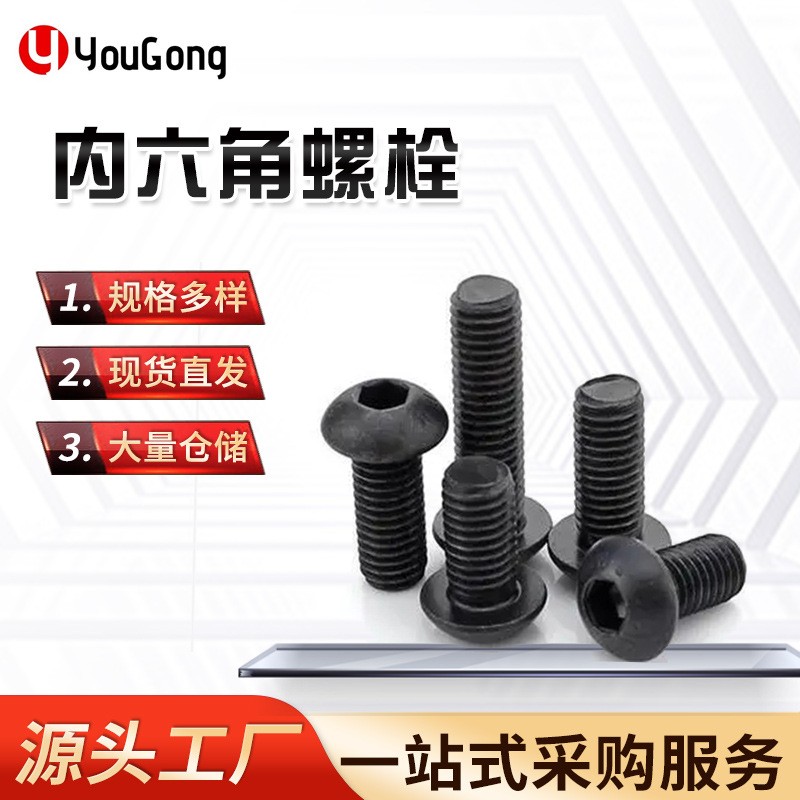
正火與退火的區別在于冷卻速度(空冷 vs 爐冷),使其具有以下優勢:
細化晶粒效果更顯著:獲得比退火更細的珠光體,硬度提高 15-20%
消除網狀滲碳體:對過共析鋼先正火再球化退火,破除二次滲碳體網
作為最終熱處理:對性能要求不高的零件(如支架、底座)直接使用
淬火溫度:
淬火介質:
介質 | 冷卻能力 | 適用鋼種 | 典型應用 |
---|
水 | 強 | 碳鋼 | 45 鋼齒輪淬火 |
鹽水 | 極強 | 高碳鋼 | T12 工具刃口淬火 |
機油 | 中等 | 合金鋼 | 35CrMoAl 氮化前淬火 |
熔融鹽 | 弱 | 精密件 | 量具分級淬火 |
淬火方法:
單液淬火:操作簡單,適用于形狀簡單件
雙液淬火:先水后油,減少開裂,用于復雜件
等溫淬火:獲得下貝氏體,強韌性優異,用于彈簧
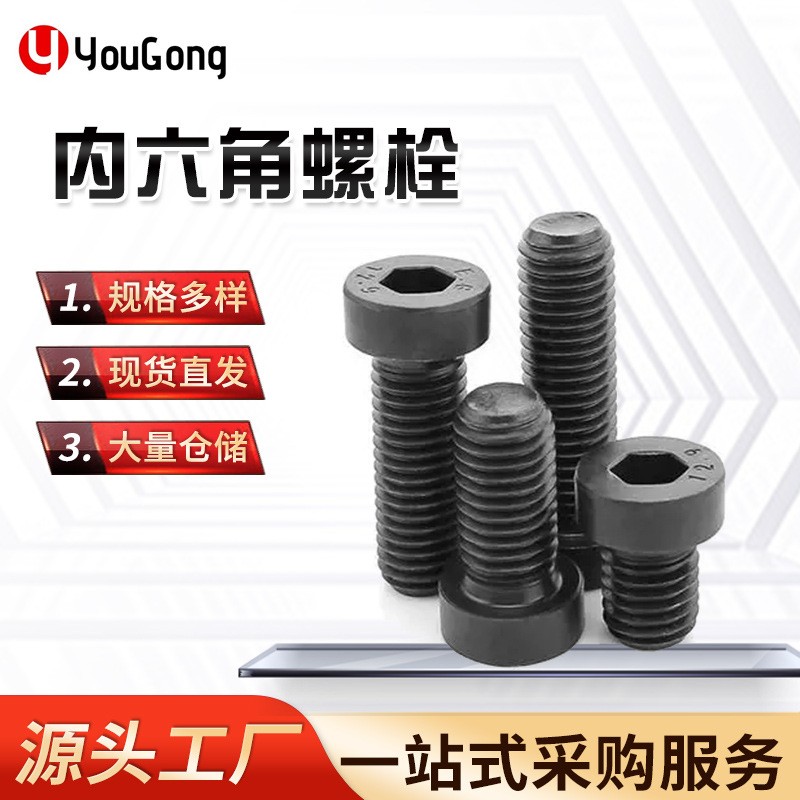
淬火后的鋼件必須及時回火(≤4 小時),根據溫度分為:
低溫回火(150-250℃):保留高硬度(HRC58-64),降低內應力,用于刀具、軸承
中溫回火(350-500℃):獲得高彈性(σb=1100-1300MPa),用于彈簧、發條
高溫回火(500-650℃):實現綜合力學性能(σb≥850MPa,A≥15%),即 "調質處理",用于軸類、齒輪
利用集膚效應實現表層快速加熱,電流頻率決定淬硬層深度:
高頻(250-300kHz):淬硬層 0.5-2mm,用于小模數齒輪(m<3)
中頻(2.5-8kHz):淬硬層 2-10mm,用于大齒輪(m=3-8)
工頻(50Hz):淬硬層 10-15mm,用于大型軸類
加熱速度快(800-1000℃/10s):晶粒細小,硬度比普通淬火高 2-3HRC
變形小、氧化少:表面光潔度保留率≥80%
疲勞強度提升:表面壓應力使疲勞極限提高 15-30%
案例:汽車半軸(40Cr)中頻淬火后,表面硬度 HRC52-56,心部 HRC30-35,壽命提升 2 倍
工藝優勢:
滲速比單獨滲碳快 30%
表層硬度更高(HRC62-66),且韌性更好
適用于承受沖擊的零件(如摩托車鏈輪)
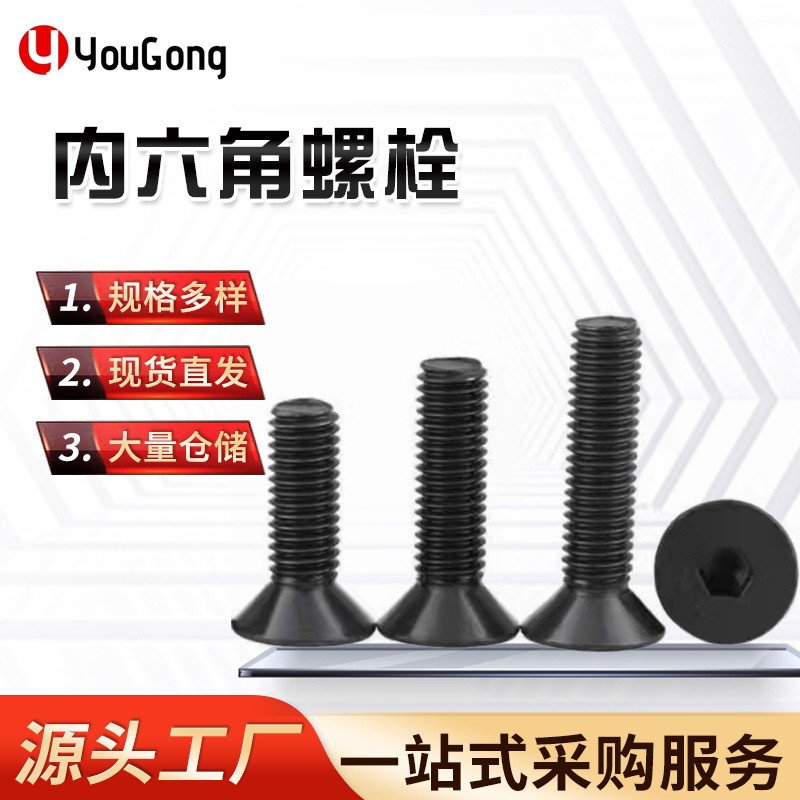
等級 | σb(MPa) | σs/σ0.2(MPa) | 硬度 (HRC) | 典型材料 | 熱處理要求 |
---|
4.8 | ≥400 | ≥320 | ≤22 | Q235 | 不熱處理 |
8.8 | ≥800 | ≥640 | 22-32 | 45 鋼 | 調質 |
10.9 | ≥1000 | ≥900 | 32-39 | 35CrMo | 淬火 + 中溫回火 |
12.9 | ≥1220 | ≥1080 | 39-44 | 42CrMo | 淬火 + 低溫回火 |
毛坯狀態控制:
鍛造件需完全退火消除網狀碳化物
冷鐓件需再結晶退火消除加工硬化
化學成分均勻性:
溫度控制精度:
箱式爐:±5℃(采用多點熱電偶實時監控)
真空爐:±3℃(適用于精密標準件)
時間控制:
采用 PLC 程序控制,誤差≤±1%
復雜件采用分段升溫,避免熱應力集中
冷卻介質管理:
首件三檢制:
外觀檢查(氧化脫碳、變形)
硬度檢測(每批抽檢 5%)
金相分析(表層 / 心部組織)
在線監測技術:
追溯系統:
每爐次記錄工藝參數,保存 3 年以上
二維碼標識實現從材料到成品的全流程追溯
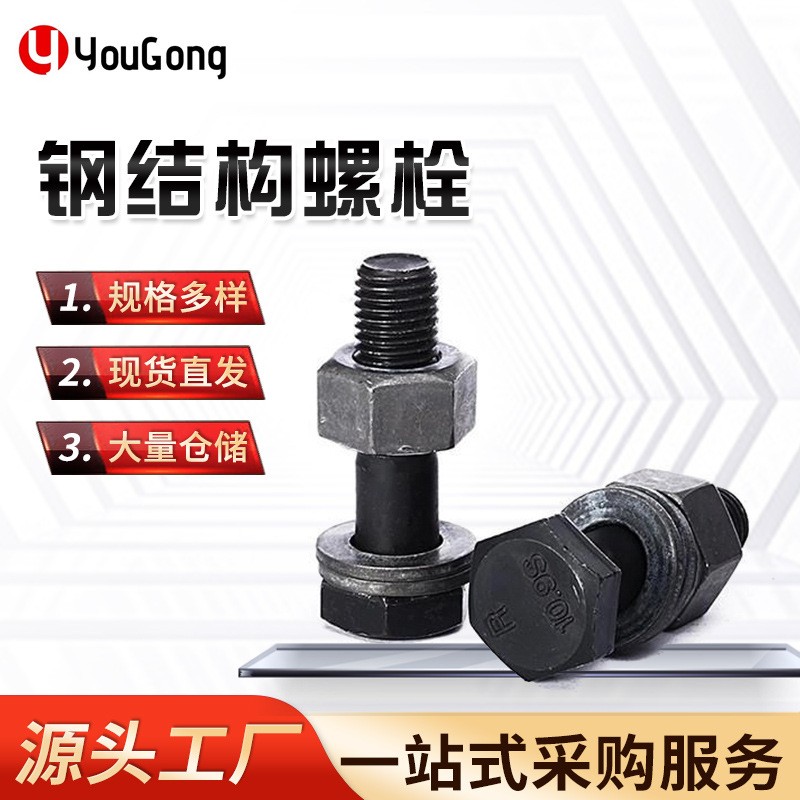
鍛造→退火→機加工→調質處理→表面處理
常規淬火回火后殘余奧氏體量≥10%,尺寸穩定性差
碳化物不均勻性導致耐磨性不一致
貝氏體等溫淬火:
深冷處理:
-120℃×12h,促進殘余奧氏體轉變
硬度均勻性控制在 ±1HRC 內
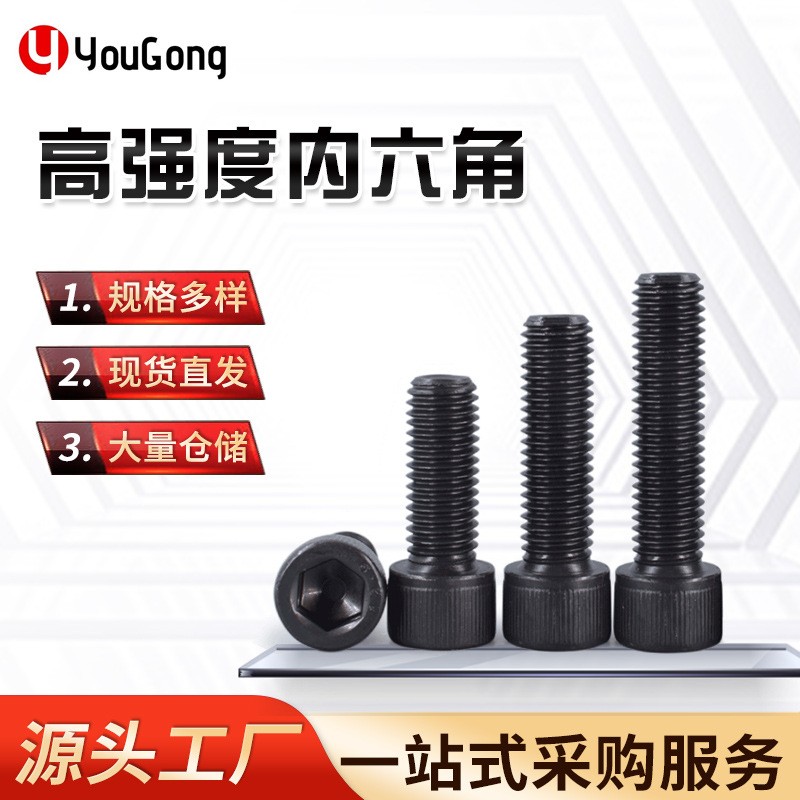
數字孿生技術:
建立工件三維模型,模擬加熱冷卻過程
預測變形量誤差≤0.05mm,減少試錯成本
工業物聯網(IIoT):
傳感器實時采集爐溫、介質流量等 100 + 參數
異常情況自動預警,工藝穩定性提升 95%
AI 工藝優化:
基于大數據分析,自動優化加熱曲線
某汽車零件熱處理良率從 82% 提升至 98%
在工業 4.0 的浪潮中,標準件已不再是簡單的通用零件,而是集成了材料科學、熱處理工藝與智能控制的精密元件。從 4.8 級到 12.9 級,每一個性能等級的跨越都凝聚著熱處理工藝的智慧結晶。對于制造企業而言,掌握熱處理工藝的核心技術,建立從材料到性能的全流程控制體系,不僅是提升產品競爭力的關鍵,更是在高端制造領域開疆拓土的核心武器。
某知名汽車零部件企業通過引入智能化熱處理系統,將發動機螺栓的疲勞壽命從 50 萬次提升至 120 萬次,成功進入國際高端供應鏈;一家軸承制造商采用貝氏體等溫淬火工藝,使滾子耐磨性提升 40%,產品單價提高 3 倍... 這些案例印證了熱處理工藝作為 "工業味精" 的重要價值。
在未來,隨著新材料、新技術的不斷涌現,熱處理工藝將繼續扮演金屬性能塑造者的角色,而標準件生產也將朝著更高精度、更高可靠性的方向邁進。對于致力于打造卓越品質的企業而言,唯有持續深化工藝理解,擁抱技術創新,才能在激烈的市場競爭中屹立潮頭,成為客戶信賴的價值伙伴。
(全文完)
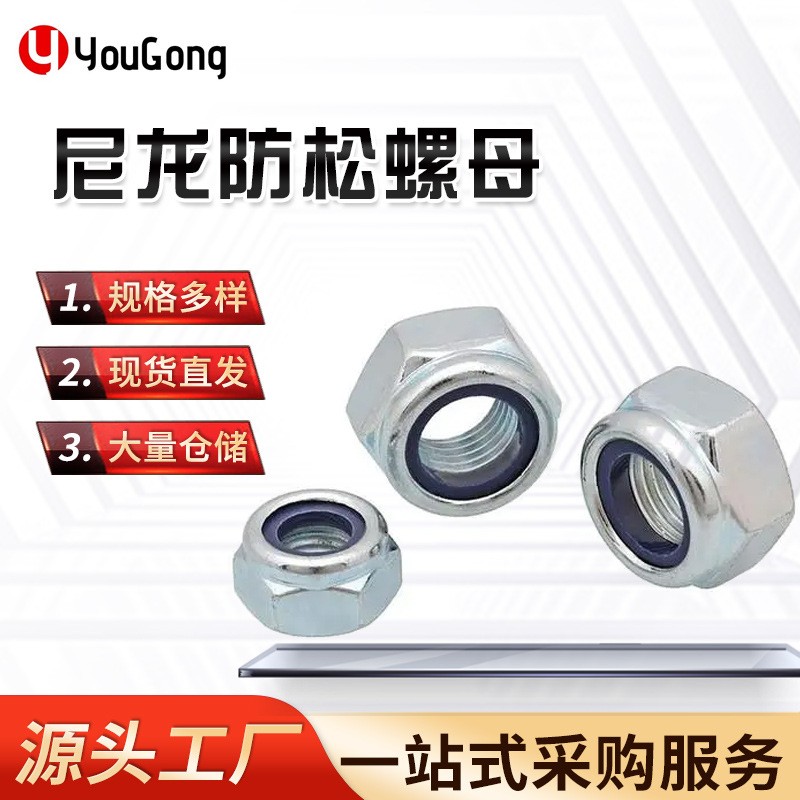
企業宣傳延展:
[企業名稱] 作為國內領先的緊固件配套解決方案提供商,擁有 30 年標準件熱處理生產經驗,配備真空爐、中頻感應加熱設備等先進裝備,建立了覆蓋 ISO、ASTM、JIS 等標準的檢測體系。我們致力于為客戶提供從材料選擇、工藝設計到性能驗證的全流程服務,助力您的產品在嚴苛工況下依然表現卓越。歡迎致電 [18330064396] 或訪問 [http://www.shush.cn/],了解更多定制化熱處理解決方案。
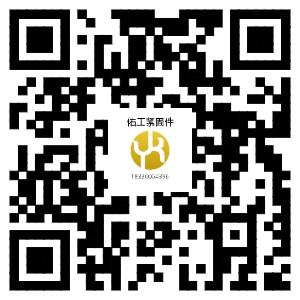